2.1. Direct blowing and foaming method
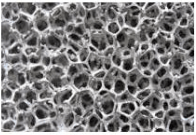
Features: simple equipment requirements, product voidage can be controlled, can achieve the continuous preparation of products.
2.2 foaming agent foaming method
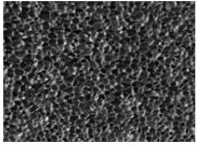
Foaming agent foaming method is: in the aluminum melt add foaming agent stirring uniform heating foaming agent decomposition of gas, gas expansion and foaming, cooling metal foam.The foaming agents used are usually hydrogen compounds such as TH2 or ZiH2.
Features: simple equipment requirements can achieve continuous product preparation.The foaming time interval of foaming agent is short, the foaming temperature is not easy to control, the bubble distribution is not uniform.
2.3 seepage casting method
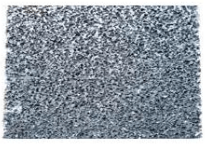
Characteristics: the preparation process aperture parameter is controllable, the through-hole rate is high, the specific surface area is large and the cost is low, suitable for large-scale industrial production.The disadvantage is that liquid metal has a high surface tension and cannot completely wet the particles and thus fill the space between the particles.
2.4 investment casting
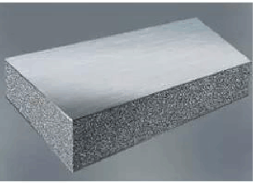
Investment casting method is the forming of polymer materials in liquid refractory material, fireproof material, filled with gap after the refractory material hardening heating decompose foam gasification, form a with the original foam in the shape of a 3 d frame, the metal aluminum pouring into the mold, the solidification after remove refractory can get with a 3 d mesh hole of aluminum foam materials.
Advantages: hole structure, good production repeatability, relatively stable density.But production is low and prices are high.